LA SALDATURA AD ARCO in GAS INERTE
con ELETTRODO INFUSIBILE DI TUNGSTENO (T.I.G. Tungsten Inert Gas)
La saldatura ad arco in gas inerte con elettrodo infusibile di tungsteno (Tungsten Inert Gas) è un procedimento in cui il calore necessario per l'esecuzione della saldatura è fornito da un arco elettrico mantenuto tra un elettrodo non consumabile ed il pezzo in lavorazione; l'elettrodo usato per condurre la corrente è un elettrodo di tungsteno o di lega di tungsteno. La zona di saldatura, il metallo fuso e l'elettrodo non consumabile sono protetti dall'influenza degli agenti atmosferici grazie al gas inerte alimentato attraverso la torcia porta elettrodo. La saldatura con procedimento TIG può avvenire con l'apporto di altro materiale (bacchetta di materiale d'apporto) oppure mediante fusione del materiale base per effetto del calore prodotto dall'arco elettrico.
- Ugello
- Pinza porta elettrodo
- Elettrodo infusibile
- Arco di saldatura
- Protezione gassosa
- Bagno di fusione
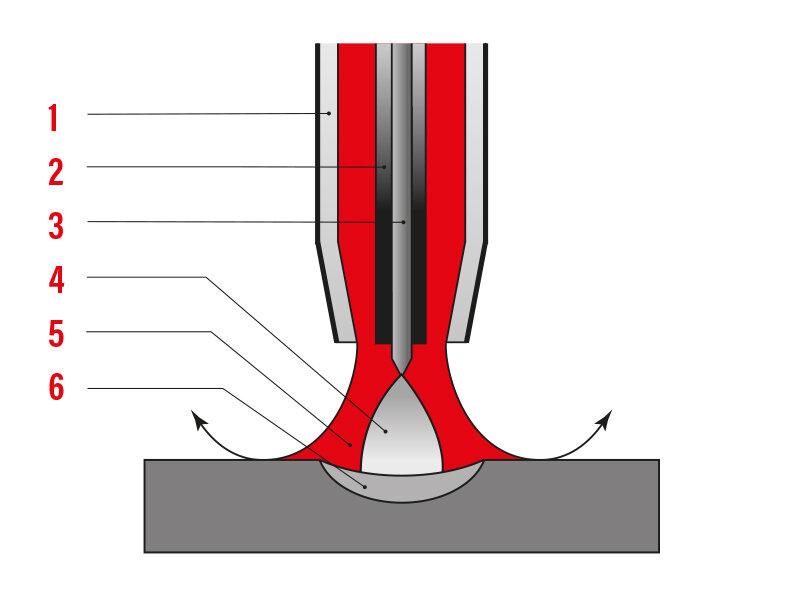
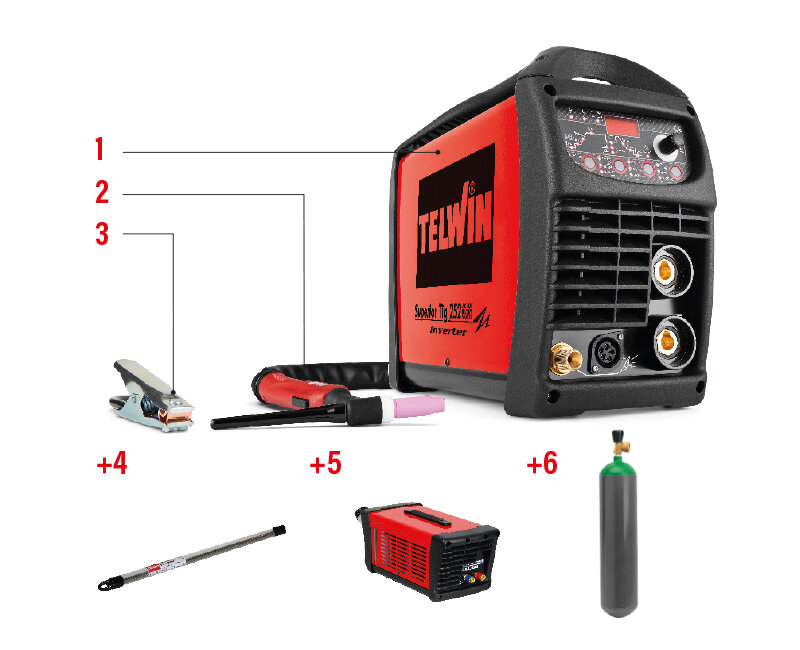
Il circuito di saldatura è essenzialmente composto dai seguenti elementi:
- GENERATORE DI CORRENTE
- TORCIA CON PORTA ELETTRODO DI TUNGSTENO
- PINZA DI MASSA
- BACCHETTA DI MATERIALE D'APPORTO
- G.R.A.
- BOMBOLA DI GAS
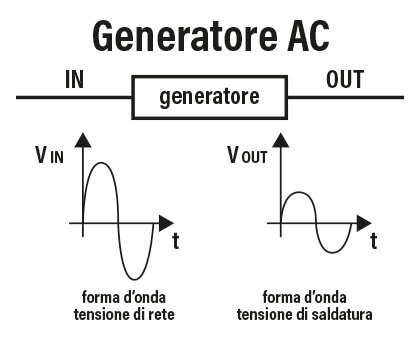
GENERATORE DI CORRENTE ALTERNATA AC (alternating current)
La corrente/tensione in uscita dal generatore assume la forma di una onda tipicamente quadra, che cambia la sua polarità ad intervalli regolari, con frequenza da 20 a 200 cicli al secondo (Hertz) o più, a seconda del tipo di generatore utilizzato. Essa è ottenuta mediante uno o più dispositivi, la cui funzione è quella di trasformare la corrente/tensione sinusoidale di rete in una adatta corrente/tensione alternata di saldatura.
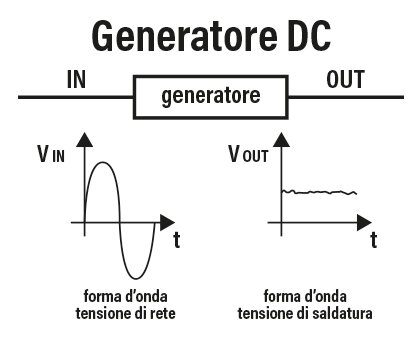
GENERATORE IN CORRENTE CONTINUA DC (direct current)
La corrente in uscita dal generatore presenta una forma d'onda continua, ottenuta tramite dispositivi che consentono la conversione della corrente/tensione da alternata a continua.
Nell'ipotesi in cui il circuito di saldatura sia costituito da un generatore di corrente continua (DC), può essere introdotta una ulteriore classificazione in funzione della modalità di connessione dei poli della sorgente di saldatura al materiale da saldare o della forma d'onda della corrente di saldatura:
- Corrente continua con collegamento in polarità diretta
Con la polarità diretta la torcia, con il relativo cavo, viene collegata al polo negativo e il materiale da saldare al polo positivo della sorgente erogatrice; in questo caso gli elettroni fluiscono dall'elettrodo verso il pezzo provocandone la fusione.
E' il tipo di corrente più utilizzata con il sistema TIG e garantisce una buona saldabilità su quasi tutti i metalli e le leghe comunemente saldabili, ad accezione dell'alluminio.. La corrente continua con polarità diretta produce un bagno di fusione stretto e profondo nonché una penetrazione decisamente superiore a quella ottenibile con la polarità inversa.
- Corrente continua con collegamento in polarità inversa
Saldando con questa polarità la torcia, con il relativo cavo, viene collegata al polo positivo e il pezzo al polo negativo della macchina erogatrice.
Questo tipo di alimentazione è scarsamente utilizzata perché produce un bagno piatto con scarsa penetrazione. La polarità inversa causa di per sé un eccessivo riscaldamento dell'elettrodo; per non provocare la bruciatura dello stesso devono essere impiegate intensità di corrente piuttosto ridotte.Si giustifica così il suo limitato impiego.
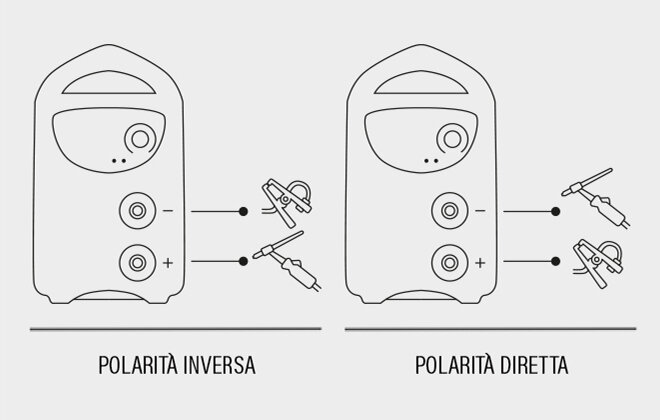
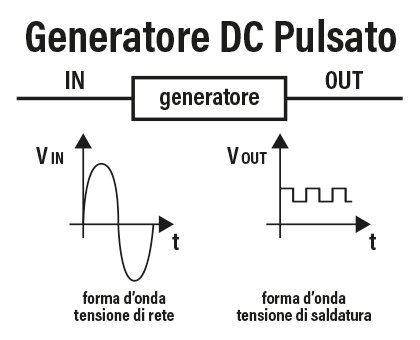
GENERATORE DC PULSATO
Esiste una ulteriore famiglia di generatori, e si identificano come generatori in corrente continua, indipendentemente dalla polarità del collegamento, e precisamente generatori in corrente continua modulata o pulsata.
Il generatore in corrente modulata è un generatore a corrente continua provvisto di particolari dispositivi che permettono la variazione dell'ampiezza della corrente di saldatura. La corrente modulata o pulsata si ottiene sovrapponendo alla corrente continua di base un'altra componente, solitamente ad onde quadre, producendo una pulsazione periodica dell'arco. Con questo sistema si ottiene un cordone di saldatura formato da una sovrapposizione continua di punti di saldatura i quali, uno dopo l'altro, formano un unico cordone. Si usa tipicamente su spessori sottili, dove bisogna controllare l'apporto di calore per evitare la perforazione del pezzo da saldare senza compromettere la penetrabilità della saldatura.