ARC WELDING IN INERT GAS
WITH NON-CONSUMABLE TUNGSTEN ELECTRODES (T.I.G. Tungsten Inert Gas)
Arc welding in an inert gas shield with a non-consumable tungsten electrode (T.I.G. - Tungsten Inert Gas or G.T.A.W. - Gas Tungsten Arc Welding) is a procedure in which the heat necessary to make the welding is supplied by an electric arc which is maintained between a non-consumable electrode and the workpiece. The electrode used to conduct the current is in tungsten or tungsten alloy. The welding zone, the melted metal and the non-consumable electrode are weatherproof thanks to the inert gas which is supplied by the electrode holder torch.
The TIG welding procedure can be used with the addition of external weld material (welding rod) or by melting the base material by means of the heat effect produced by the electric arc.
- Nozzle
- Electrode holder clamp
- Infusible-electrode
- Welding arc
- Gaseous protection
- Melting pool
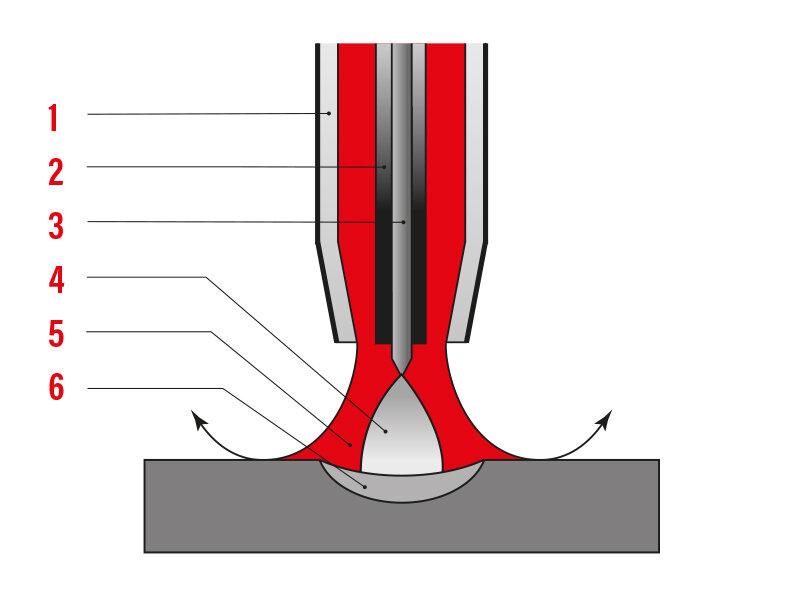
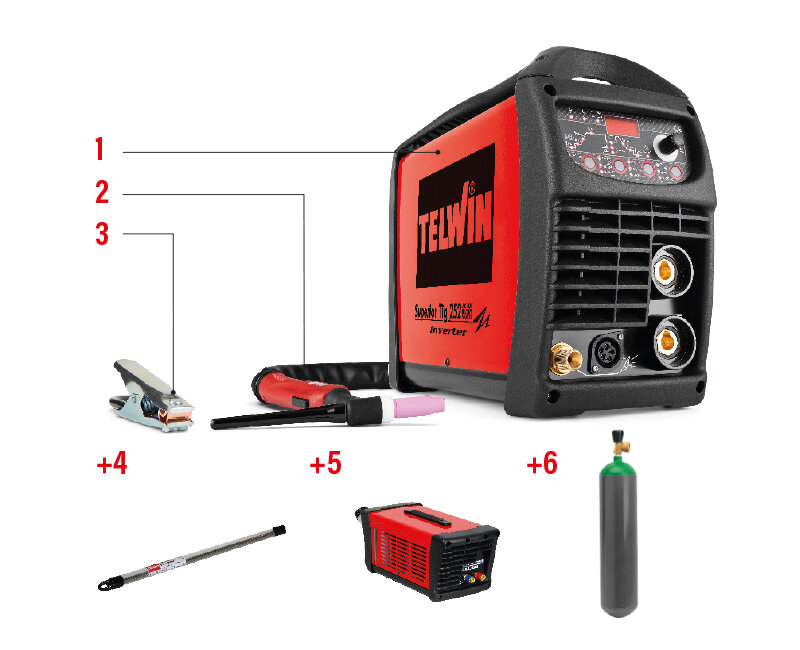
The welding circuit consists essentially of the following elements:
- POWER SOURCE
- TUNGSTEN ELECTRODE-HOLDER TORCH
- EARTH CLAMP
- WELDING ROD
- WATER COOLING SYSTEM
- GAS CYLINDER WITH PRESSURE CIRCUIT
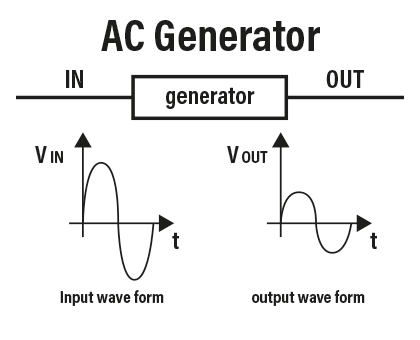
ALTERNATING CURRENT (AC) POWER SOURCE
The output current/voltage from the power source takes the typical form of a square wave, which changes its polarity at regular intervals with a frequency of 20 up to 200 cycles per second (Herz) or more, depending on the type of power source used. This is achieved by means of one or two devices whose function is to transform the current/voltage sine wave from the distribution network into a suitable alternating welding current/voltage.
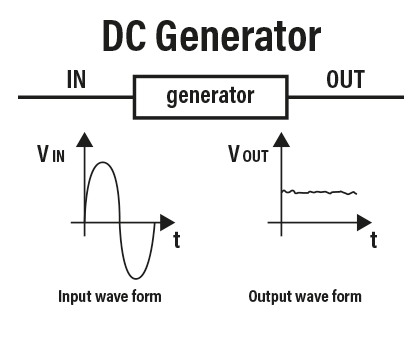
DIRECT CURRENT (DC) POWER SOURCE
The output current from the power source has a continuous wave form, which is obtained by means of devices that are able to convert the current/voltage from alternating to direct.
If the welding circuit consists of a direct current power source (DC), it can be further classified according to the method of connecting the power source poles to the material to be welded or the form of the welding current:
- Straight polarity connection
With staright polarity connection, the torch and its cable is connected to the negative pole and the material to be welded to the positive pole of the power source; in this case the electrons flow from the electrode towards the piece, causing melting. This is the most frequently used type of current with the TIG system and it ensures good weldability for almost all commonly weldable metals and alloys, with the exception of aluminium. Direct current with straight polarity produces a narrow, deep weld pool and also a penetration that is decidedly better than that obtainable with reverse polarity.
- Reverse polarity connection
When welding with this polarity the torch with its cable is connected to the positive pole and the piece to the negative pole of the power source.
This type of power supply is rarely used because it produces a flat weld pool with poor penetration. Reverse polarity in itself causes excessive heating of the electrode, and to prevent the electrode from burning, rather low current intensities should be used. This is the reason for its limited use.
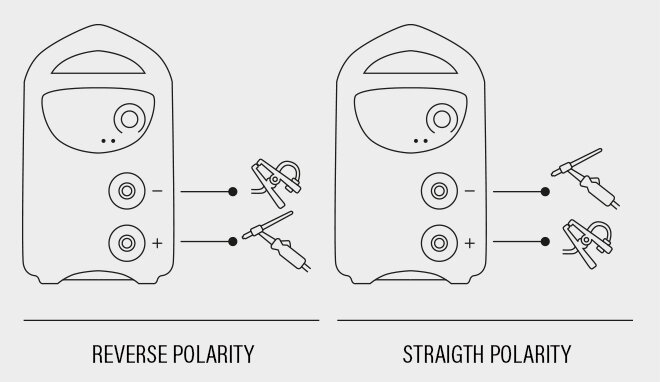
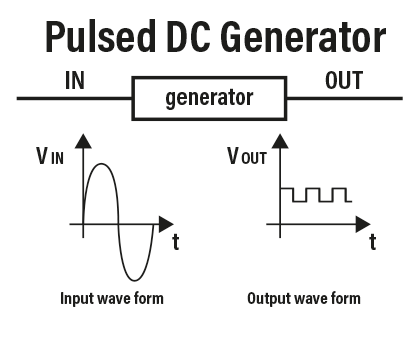
PULSED DC GENERATOR
There is a further family of power sources, identified as direct current power sources irrespective of the polarity of the connection and named as modulated or pulsed direct current power sources.
The modulated current power source is a direct current power source fitted with particular devices used to vary the size of the welding current. Modulated or pulsed current is obtained by the superimposition on the direct base current of a further component, usually a square wave form, to produce a periodic pulsation of the arc.With this system a weld seam is obtained consisting of a continuous superimposition of spot welds that consecutively form a single seam. This method is typical of welds on thin materials where it is necessary to control the amount of heat so as to prevent the piece being perforated without diminishing the penetrability of the weld.