A SOLDADURA POR ARCO em GÁS INERTE
com ELÉCTRODO INFUSÍVEL DE TUNGSTÉNIO (T.I.G. Tungsten Inert Gas)
A soldadura por arco em gás inerte com eléctrodo infusível de tungsténio (Tungsten Inert Gas) é um processo no qual o calor necessário para a execução da soldadura é fornecido por um arco eléctrico mantido entre um eléctrodo não consumível e a peça em processamento; o eléctrodo usado para conduzir a corrente é um eléctrodo de tungsténio ou de liga de tungsténio. A área de soldadura, o metal fundido e o eléctrodo não consumível são protegidos pela influência dos agentes atmosféricos graças ao gás inerte alimentado mediante a tocha porta-eléctrodo. A soldadura com processo TIG pode ocorrer com a adição de outro material (vareta de material de adição) ou mediante a fusão do material base por efeito do calor produzido pelo arco eléctrico.
- Bico
- Pinça porta-eléctrodo
- Elétrodo infusível
- Arco de soldadura
- Proteção gasosa
- Baho de fusão
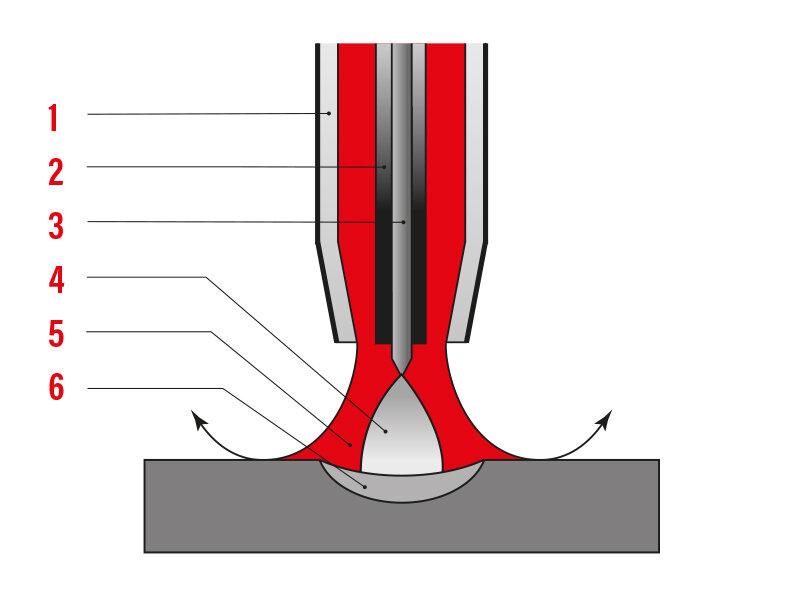
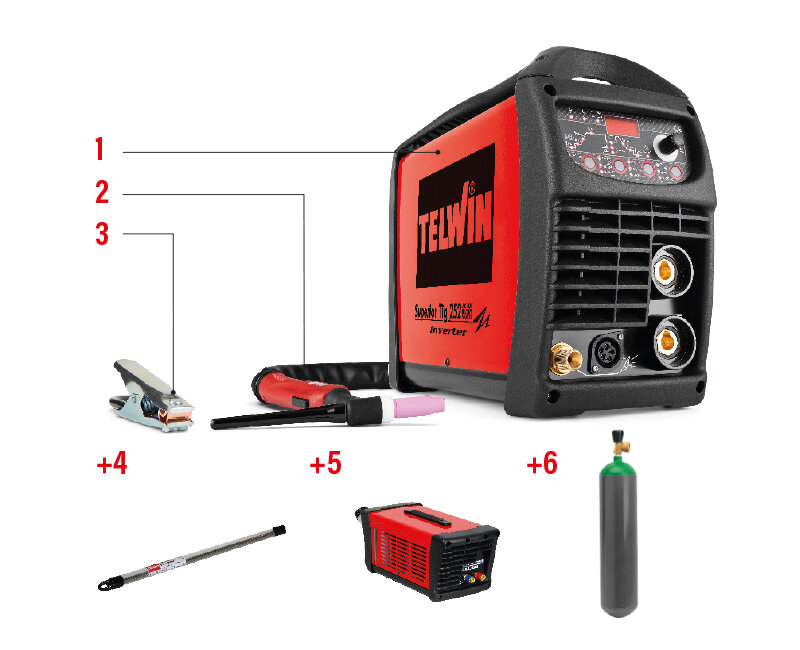
O circuito de soldadura é composto essencialmente pelos elementos a seguir:
- GERADOR DE CORRENTE
- TOCHA PORTA-ELÉCTRODO DE TUNGSTÉNIO COM FEIXE DE CABOS
- PINÇA COM CABO DE MASSA
- VARETA DE MATERIAL DE ADIÇÃO
- CONJUNTO DE ARREFECIMENTO A ÁGUA
- CILINDRO DE GÁS COM CIRCUITO DE PRESSÃO
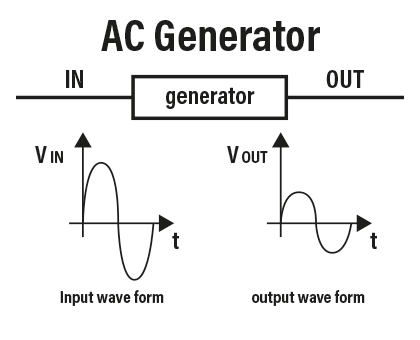
GERADOR EM CORRENTE ALTERNADA AC (alternating current)
A corrente/tensão de saída do gerador assume a forma de uma onda tipicamente quadrada, que muda a sua polaridade em intervalos regulares, com frequência de 20 ou 200 ciclos por segundo (Hertz) ou mais, conforme o tipo de gerador utilizado. Ela é obtida mediante um ou mais dispositivos, cuja função é a de transformar a corrente/tensão sinusoidal de rede em uma corrente/tensão alternada apropriada de soldadura.
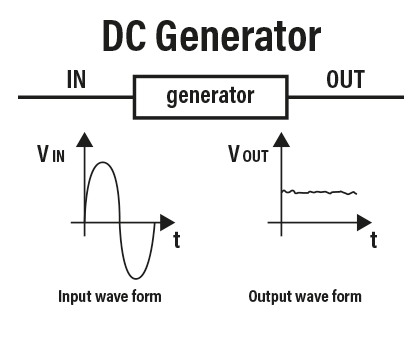
GERADOR EM CORRENTE CONTÍNUA DC (direct current)
A corrente na saída do gerador apresenta uma forma de onda contínua, obtida através de dispositivos que permitem a conversão da corrente/tensão de alternada para contínua.
No caso em que o circuito de soldadura seja composto por um gerador de corrente contínua (DC), pode ser introduzida mais uma classificação em função da modalidade de conexão dos pólos da fonte de soldadura ao material a soldar ou da forma de onda da corrente de soldadura:
- Corrente contínua com ligação em polaridade directa
Com a polaridade directa a tocha, com o relativo cabo, é ligada ao pólo negativo e o material a soldar ao pólo positivo da fonte abastecedora; nesse caso os electrões fluem do eléctrodo para a peça provocando a sua fusão. É o tipo de corrente mais utilizado com o sistema TIG e garante uma boa soldabilidade em quase todos os metais e as ligas normalmente soldáveis, com excepção do alumínio. A corrente contínua com polaridade directa produz um banho de fusão estreito e profundo e também uma penetração decididamente superior àquela que pode ser obtida com a polaridade inversa.
- Corrente contínua com ligação em polaridade inversa
Soldando com essa polaridade a tocha, com o relativo cabo, é ligada ao pólo positivo e a peça ao pólo negativo da máquina abastecedora.Esse tipo de alimentação é pouco utilizado porque produz um banho chato com penetração escassa. A polaridade inversa causa por si só um aquecimento excessivo do eléctrodo; para não provocar a queimadura dele devem ser utilizadas intensidades de corrente mais reduzidas. Justifica-se assim o seu uso limitado.
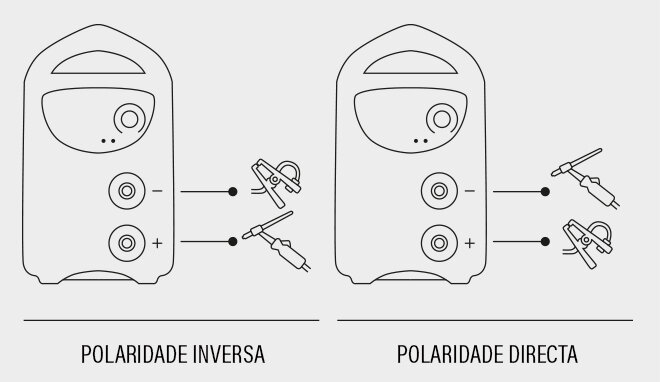
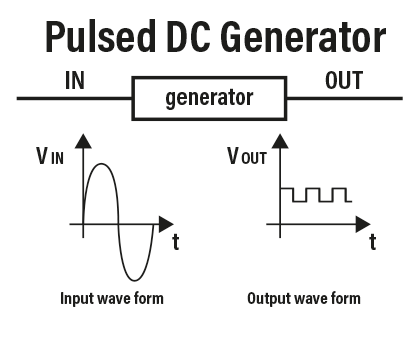
GERADOR DC PULSADO
Existe mais uma família de geradores, e se identifica como geradores em corrente contínua, independentemente da polaridade da ligação, e exactamente geradores em corrente contínua modulada ou pulsada. O gerador em corrente modulada é um gerador com corrente contínua equipado com dispositivos específicos que permitem a variação da amplitude da corrente de soldadura. A corrente modulada ou pulsada é obtida sobrepondo à corrente contínua de base um outro componente, geralmente de ondas quadradas, produzindo uma pulsação periódica do arco. Com esse sistema se obtém um cordão de soldadura formado por uma sobreposição contínua de pontos de soldadura, os quais, um após o outro, formam um cordão único. Usa-se tipicamente em espessuras finas, onde é necessário controlar o fornecimento de calor para evitar a perfuração da peça a soldar sem comprometer a penetrabilidade da soldadura.